Leak Test Fixture Design: How To Do It Right
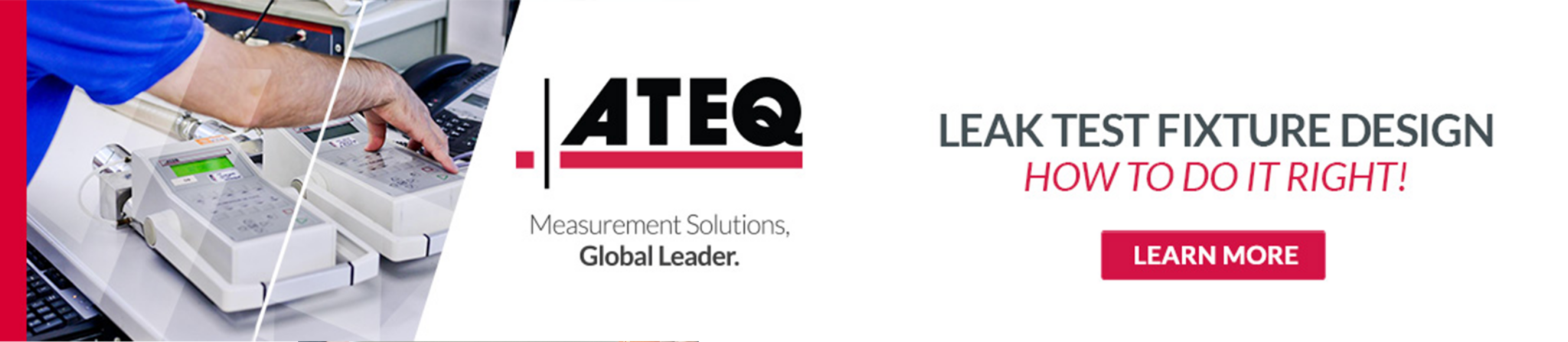
Importance of Good Leak Test Fixture Design
The design of your leak test fixture can make or break the performance of your leak testing instruments and your test results.
A poor design will negatively impact your test’s accuracy, efficiency, and repeatability.
This article will discuss several factors and best practices that must be considered when designing a leak test fixture and why they matter.
Seals
The improper design of seals is one of the foremost reasons for inaccurate test results.
This is why having the correct seal for your specific application and the type of leak test being performed is key. Proper seal design will result in a shorter stabilization time and will decrease the chance of test-altering volumetric changes.
Seals can be separated into two main categories: mechanical or manual (hand-operated).
A mechanical (pneumatic) seal is initiated by air and physically deformed to provide a mechanical lock. A mechanical seal is typically used in automated leak testing. A manual seal is usually located physically on the part being tested and is actuated manually by an operator on the production floor.
There are several factors to consider when it comes to choosing the correct seal design for your specific test fixture, such as:
Hardness:
- The hardness of the seal refers to the resistance of the seal material to denting or becoming misshapen.
- A seal’s hardness is measured in units of Shore, and the typical range (for leak testing) is from 40 to 70 shore.
- Note: If the hardness rating of a seal is too high, it will decrease the sealing effectiveness and increase maintenance difficulty.
Groove Fit:
- Use tight grooves on the test fixture to contain the gasket or seal and to minimize unwanted movement and deformation.
- An O-ring is used to block a path that may allow gas or liquid to escape.
- Groove size should be based on the geometry of the O-ring.
Customization:
- When a DUT (device under test) has a complicated shape, a customized molded seal will perform better than a regular O-ring.
- Well-balanced and tightly secured molded seal designs with O-rings create minimal contact at the point of seal, allowing for an adequate seal at a lower force.
- The seal should be designed to be easily replaceable and easily visible enough to enable troubleshooting with soapy water, as worn seals are a common problem.
Fixture Structure
Fixture design is paramount for making certain that your leak test results are as accurate as possible and have better repeatability. There are a lot of different factors to consider when designing a test fixture. The fixture should be made of rigid materials as this will prevent excess movement and changes in volume when testing a part due to the fixtures’ flexibility.
Correct fixture design can improve the speed of your stabilization times, shorten test cycle time, and increase accuracy through reduced large test volume. Correct fixture design can also reduce wear on your seals, eliminate the dead volume and increase the life of your seals. Temperature, Volume, Hard stops, and Connectors should all be considered when designing your leak test fixture.
Temperature:
- Applying thermal insulation outside the test fixture helps to avoid thermal effects such as cold air drafts.
- Tying and insulating the test and reference tubes together will make sure that they are always located under the same environmental conditions.
- The test area should be isolated from any kind of temperature sources such as wind, a/c, or sunlight.
Volume:
- Design the chamber contour so that the instrument will be closer in proximity to the test part.
- Use aluminum filler blocks, because it conducts heat and will help reduce stabilization time.
- Reduce the length of the tubes as this will ensure faster cycle times.
Hard Stops:
- When fixtures are driven by an air cylinder an external hard stop can help prevent movement from the seal when it’s being compressed, extending the longevity of the seal, and decreasing stabilization time.
- Springs (lip seals) can also be added to control force against the part and cope with tolerance uncertainties.
- Hard stops help prevent the internal dead volume from behaving like a porous material.
Fixture Connections:
- Thread connections should be glued on the first thread in contact with the test air, to prevent false leak readings.
- Connections should be secure but not overly tightened so that the fitting will not become damaged.
- Adding quick couplers can help quickly switch between test chambers or dismount the test chamber from the leak tester.
At ATEQ our high-quality leak test connectors are the preferred choice for easy leak testing detection. Learn more about our quick couplers here.
Machine Design
Last but certainly not least is the machine design which is essentially the foundation of the leak test station. Proper machine design should include a sturdy frame, that helps to protect the test fixture areas from vibrations, oil, air drafts, water, and debris. When considering the appropriate machine design, one should look at factors such as environmental conditions and high pressure best practices:
Environmental Conditions:
- A safety curtain is recommended to be installed between the operator and the fixture. Operators should also wear gloves when manually unloading/ loading test parts. This will ensure protection against thermal effects or exchange from the human body and thermal radiation.
- The fixture and device under testing need to be in dry stable temperatures when testing. Also, a high-quality air filter should be used to ensure that the compressed air remains clean and free of contamination.
- Compressed air needs to be at the same temperature as the test fixture and the part to prevent changes in temperature that would negatively impact stabilization.
High Pressure Best Practices:
- Use an air tank buffer for better consistency.
- Because high pressure generates heat, use prefill and pre-dump to cancel heating.
- To avoid damage to the test instrument due to accidental overpressure on the air supply install Y- valves in the circuit.
Have Questions? Want to Learn More?
Contact an ATEQ Expert today!
Or sign up for our Leak Test Academy to get in-depth leak test fixture design training!
Leave A Comment
You must be logged in to post a comment.